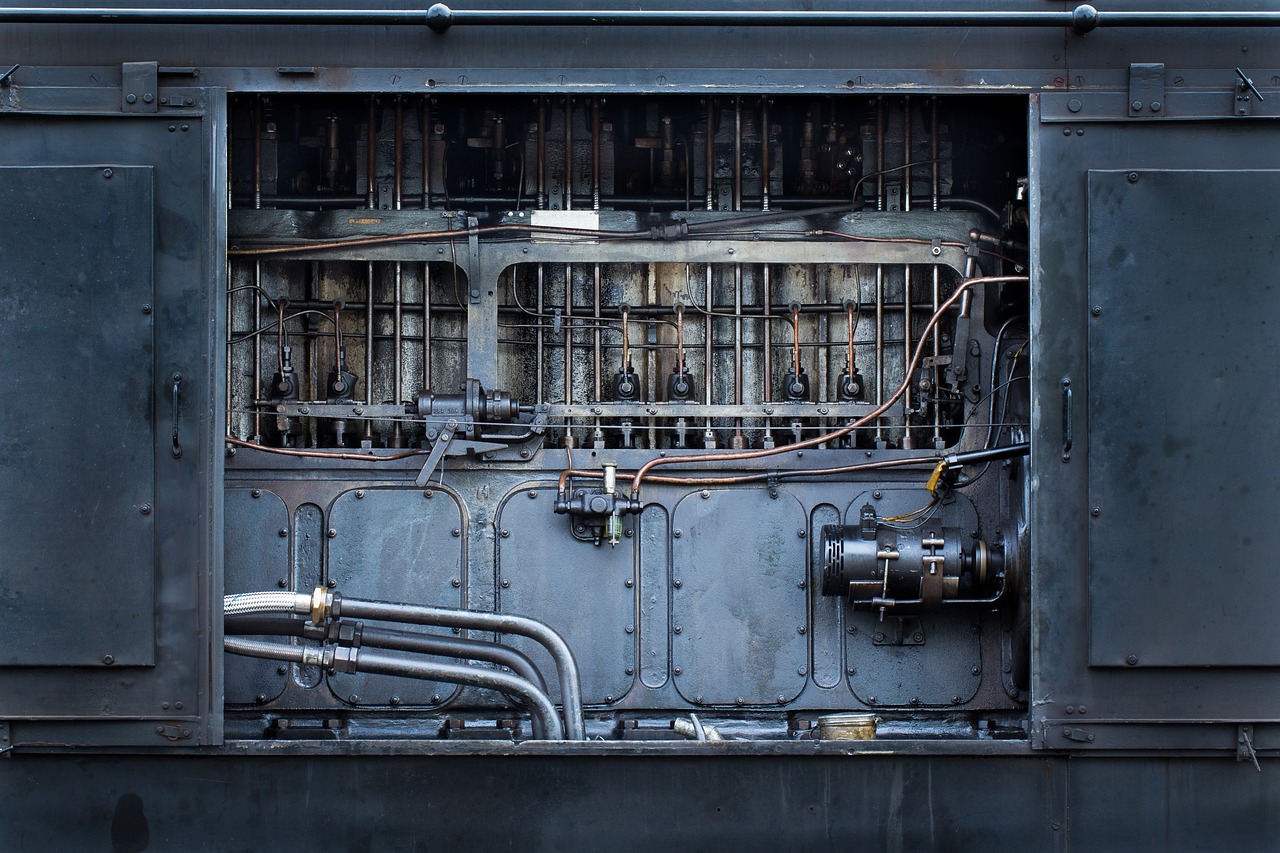
Special Purpose Machines
Needs Analysis and Feasibility Study
Requirements Gathering
The design process begins with a thorough needs analysis to understand the specific requirements of the SPM. This involves close collaboration with the client to determine the desired production rate, product specifications, and any unique process limitations.
Technical Feasibility
Once the requirements are clear, a feasibility study is conducted to assess the technical viability of the project. This includes evaluating existing technologies, identifying potential design challenges, and exploring alternative solutions.
Cost and Time Estimation
The feasibility study also involves estimating the cost and time required to design, manufacture, and implement the SPM. Engineering Excellence in Machinery This provides a realistic assessment of the project’s financial and scheduling feasibility.
Conceptual Design and Design Optimization.
Initial Concept Development
Based on the needs analysis and feasibility study, a preliminary concept is developed. Custom Machine Design This involves outlining the machine’s overall layout, identifying key components, and exploring different design approaches.
Simulation and Analysis
Computer-aided design (CAD) software is used to create detailed 3D models of the SPM. These models are then subjected to rigorous simulation and analysis to evaluate performance, strength, and reliability under various operating conditions.
Design Optimization
Industrial Automation Solutions . The design is iteratively refined based on the simulation results, incorporating feedback from engineers and clients. The goal is to optimize the design for maximum efficiency, accuracy, and durability.
Component Selection and Sourcing
Component Specification
The selection of components is crucial to ensure High-Performance Machinery the SPM’s performance and reliability. This involves carefully considering factors such as material properties, precision tolerances, load capacity, and environmental conditions.
Sourcing and Procurement
Components are sourced from reputable suppliers based on their quality, availability, and pricing. The procurement process involves negotiating contracts, managing inventory, and ensuring timely delivery for Tailored Industrial Machines.
Quality Control
Incoming components are thoroughly inspected to ensure they meet the specified quality standards. This is essential to prevent defects from being incorporated into the final machine.
Component Integration
Specialized Manufacturing Equipment, The selected components are integrated into the SPM according to the optimized design. This involves carefully assembling, aligning, and securing the components to ensure proper functionality.
Manufacturing and Assembly
Fabrication
The SPM’s components are fabricated using various manufacturing processes such as machining, casting, molding, and welding. These processes require specialized equipment and skilled technicians to achieve the required precision and quality.
Assembly
Once the components are fabricated, they are assembled into the final SPM. This involves carefully aligning, securing, and testing the components to ensure proper functionality and performance.
Testing and Commissioning
Custom Automated Systems, The completed SPM undergoes rigorous testing to verify its performance, accuracy, and reliability. This may involve simulating real-world operating conditions and measuring critical performance parameters.
Quality Assurance and Validation
Inspection | Throughout the design, manufacturing, and assembly process, quality assurance measures are implemented to ensure that the SPM meets the specified requirements. |
Testing | The SPM undergoes rigorous testing to verify its performance, accuracy, and reliability. This may involve simulating real-world operating conditions and measuring critical performance parameters. |
Documentation | Detailed documentation is maintained throughout the project, including design specifications, manufacturing procedures, and test results. This documentation serves as a reference for future maintenance and upgrades. |
Installation and Training
Site Preparation
The SPM is delivered to the client’s facility, where it is carefully installed and integrated into the existing production line. This involves preparing the site, ensuring proper power and utilities, and providing adequate workspace.
Machine Installation
The SPM is carefully installed according to the provided specifications. This may involve aligning the machine, securing it to the floor, and connecting it to the production line.
Operator Training
Operators are provided with comprehensive training on the operation and maintenance of the SPM. This ensures that they are able to operate the machine safely and efficiently, maximizing its potential.
Post-Installation Support
Special Purpose Equipment and Automated Production Systems Ongoing support is provided to the client to address any issues that may arise during the initial operation of the SPM. This may involve troubleshooting, technical assistance, and providing spare parts as needed.
Maintenance and Upgrades
Preventative Maintenance
Industrial Custom Machines Regular maintenance schedules are established to ensure the SPM’s continued performance and reliability. This involves inspecting components, lubricating moving parts, and replacing worn-out parts to prevent breakdowns.
Corrective Maintenance
When breakdowns occur, the SPM is promptly repaired to restore its functionality. This may involve diagnosing the problem, sourcing replacement parts, and performing repairs according to established procedures.
Technology Upgrades
As technology advances, SPMs may require upgrades to improve performance, efficiency, or safety. This could involve replacing outdated components, integrating new technologies, or modifying software to meet evolving requirements.
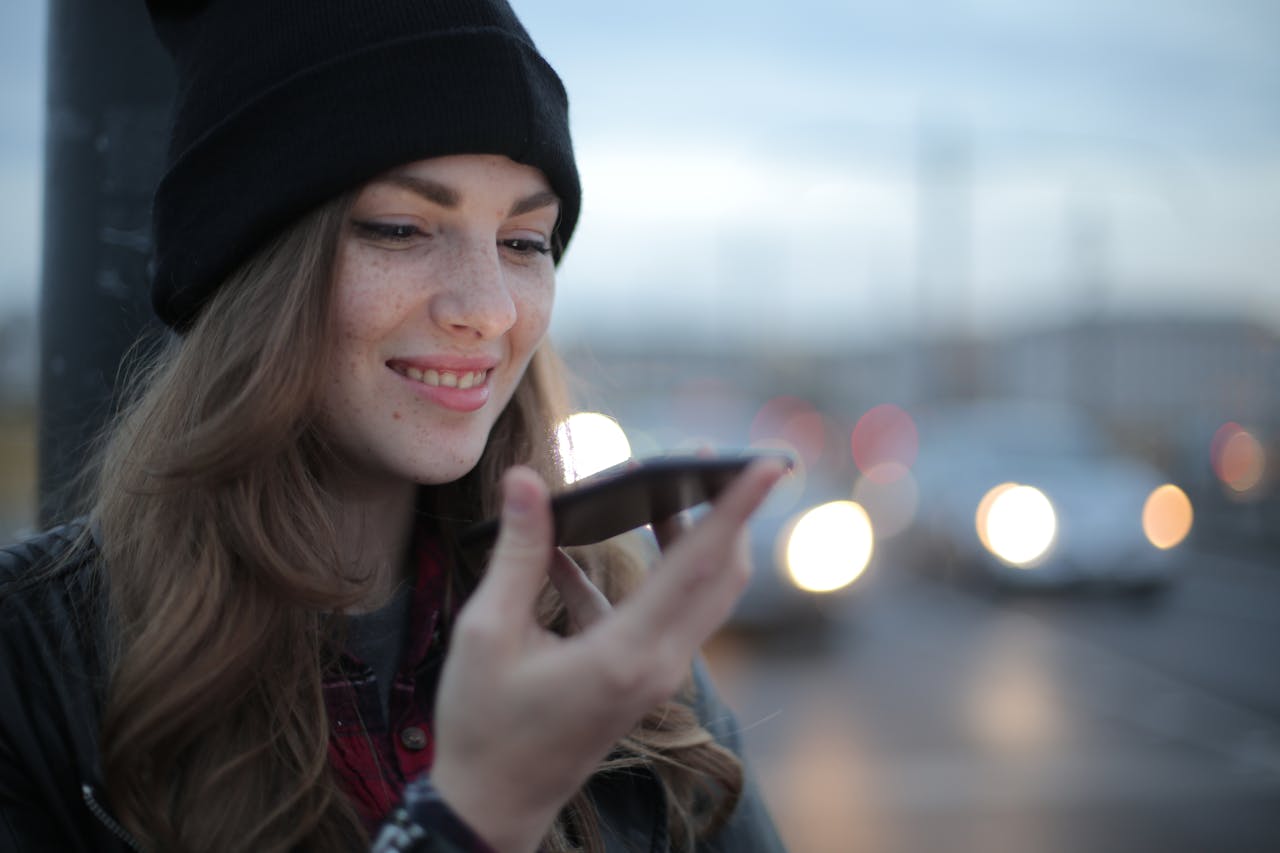
Get In Touch
Let’s bring your vision to life.